Composite parts
GRP and CFRP parts in maximum precision
Modern fiber composite technology is not only in demand in yacht building, but also in the manufacture of synthetic components of all kinds. Knierim Yachtbau therefore also offers the construction of composite parts of all kinds.
Whether equipment carriers, radar masts, millimeter-precise outer skin flaps or elaborate deck furniture and pool landscapes, we build every free-form shape true to the designer's specifications. The molds are milled using one of our three 5-axis milling machines. We then use this to produce the high-tech GRP sandwich components using vacuum technology in accordance with our laminate plans. We take functional and design-related detailed solutions such as ventilation shafts, stainless steel work, the installation of kitchen appliances or electronics into account right from the construction stage. We will be happy to supply you with the component with a final painted surface - according to your interests and requirements.
Thanks to its experience with various new builds in carbon, Knierim is a specialist in the processing of carbon fiber. Knierim uses this material to produce super-light cockpit tables, bowsprits, instrument covers and much more. For this purpose, a mold is made individually and the component is then produced from it. In this way, small batches of certain parts can also be produced, e.g. for series production boats.
The foundation for all types of synthetic parts are precise master models, which Knierim produces through its subsidiary Knierim Tooling.
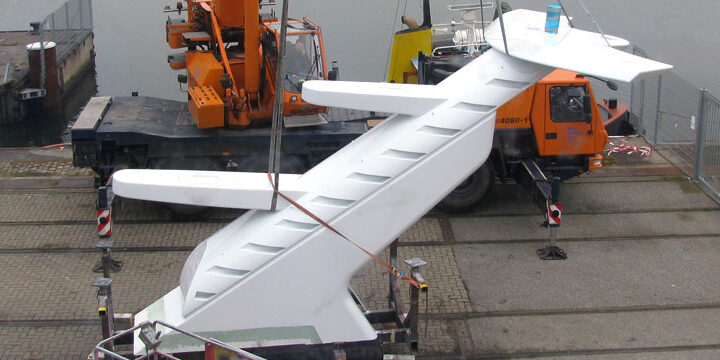
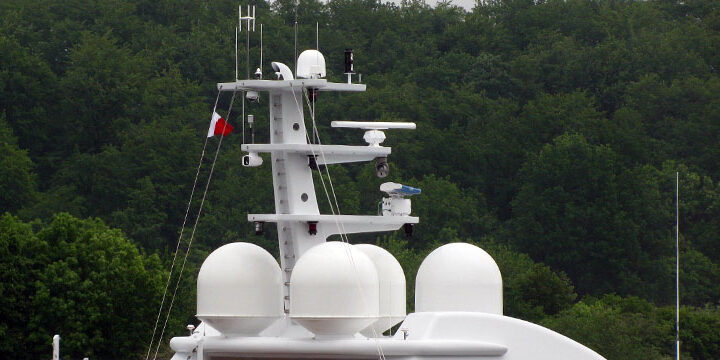
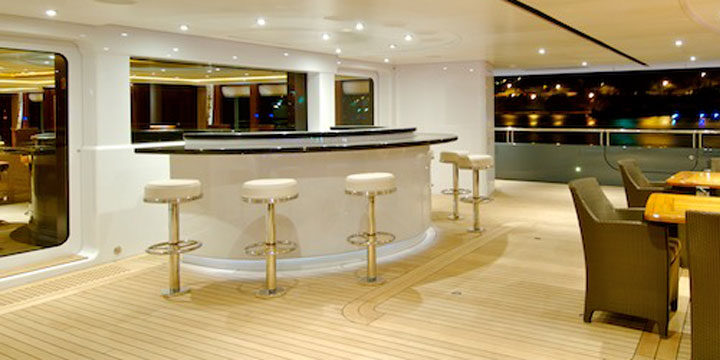
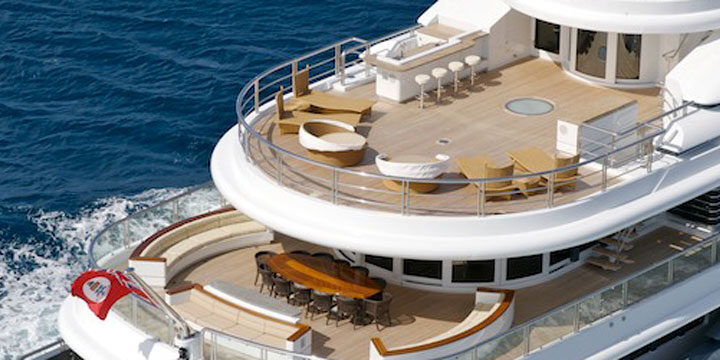
Knierim Tooling
Precision thanks to 5-axis milling machine
